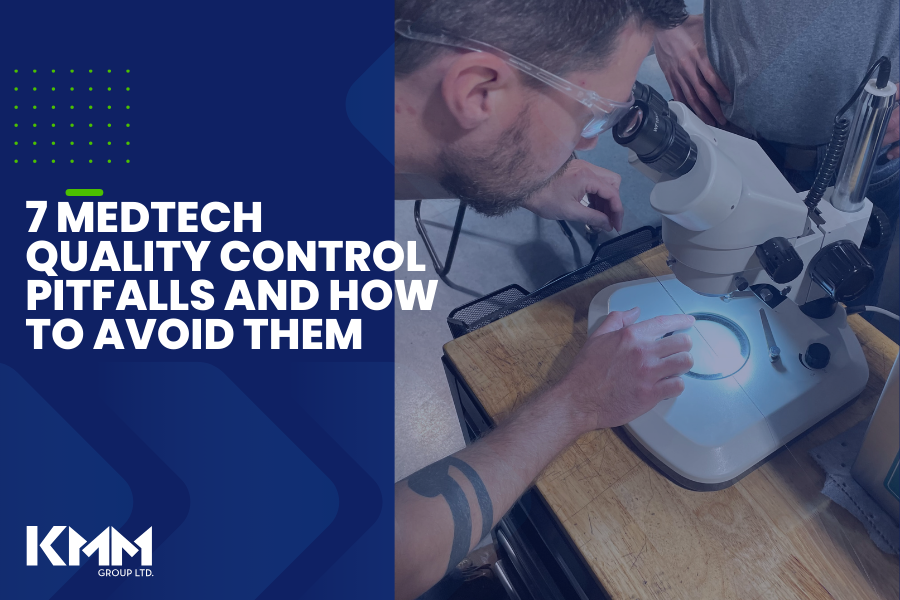
Quality control (QC) in MedTech manufacturing is a balancing act between precise tolerances, meeting regulatory standards, and keeping production on schedule. But even with the best processes in place, small oversights can lead to inefficiencies, rework, or delays.
The good news? Many common QC pitfalls are avoidable with the right approach. By recognizing these challenges early, you can streamline your operations, improve product reliability, and stay ahead of potential issues before they become real problems.
Let’s explore seven key QC pitfalls and how to sidestep them for smoother, more efficient production.
Potential QC Failures to Identify and Prevent
1. Inadequate Supplier Qualification
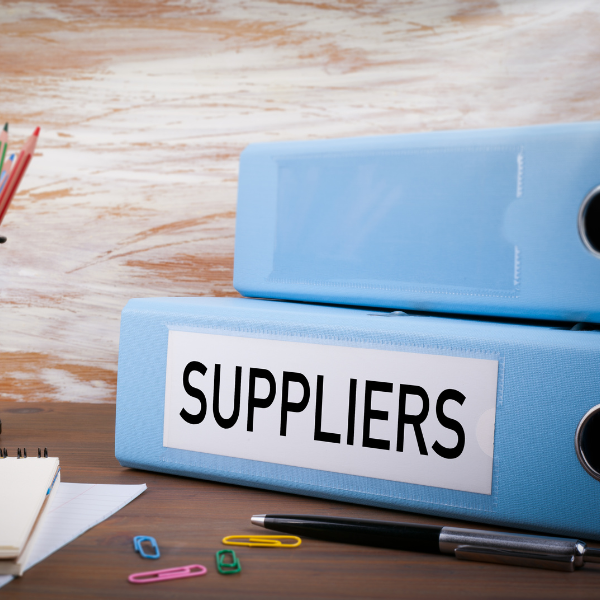
The Risk:
Failing to vet suppliers properly can lead to inconsistent raw material quality, affecting the final product’s performance.
Solution:
Implement a robust supplier assessment program, including on-site audits and material testing.
2. Insufficient Supplier Quality Management
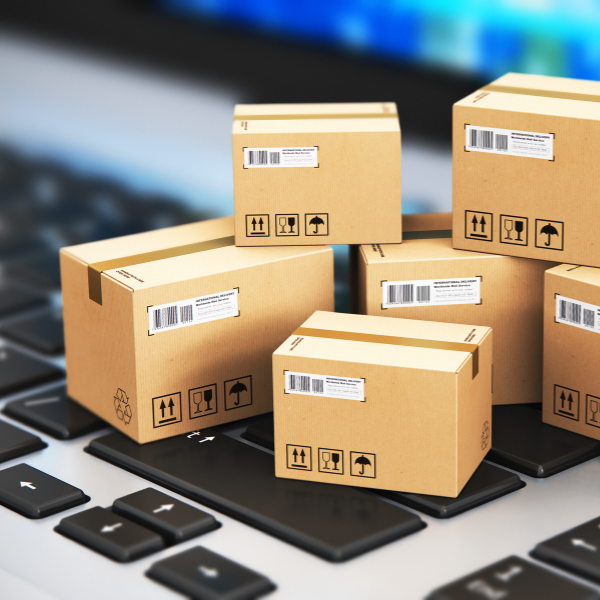
The Risk:
Many quality issues stem from unreliable suppliers, affecting material consistency and product integrity.
Solution:
Establish rigorous supplier qualification and monitoring programs. Conduct regular audits and demand adherence to ISO 13485 standards. Develop long-term partnerships with trusted suppliers for high-precision components.
3. Poor Documentation and Traceability
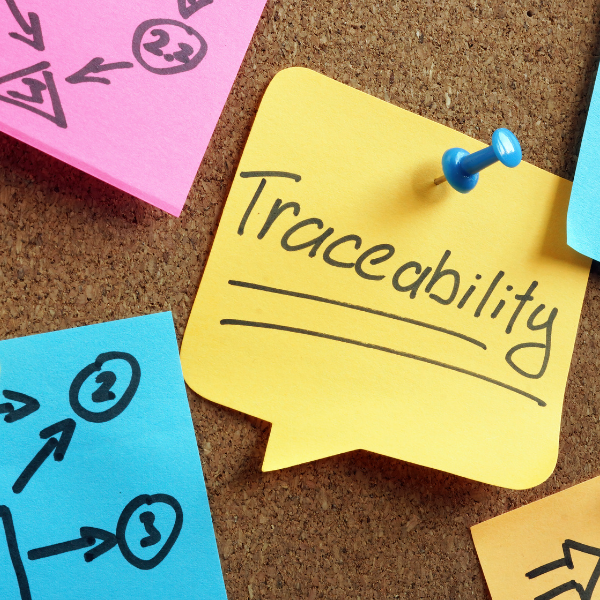
The Risk:
Regulatory bodies require detailed documentation to track production history, failures, and corrective actions. Incomplete or inaccurate documentation can result in compliance failures during FDA or ISO 13485 audits.
Solution:
Utilize electronic documentation systems to track and maintain accurate records in real time.
4. Inadequate Process Validation
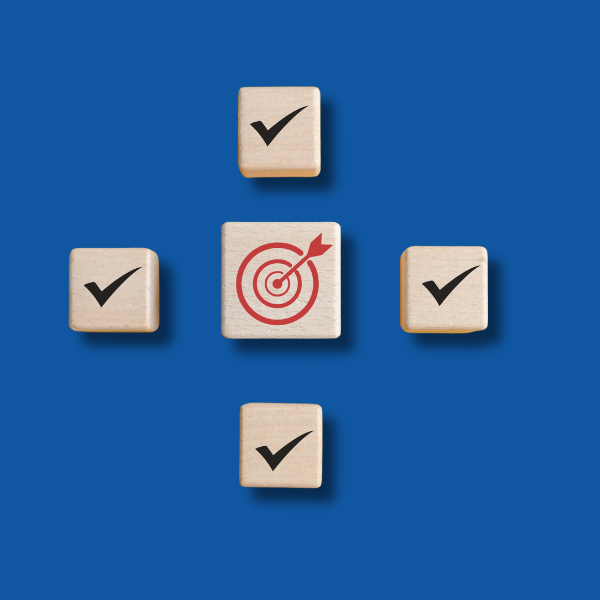
The Risk:
Process validation ensures manufacturing consistency, but poor validation can lead to defects and compliance issues.
Solution:
Follow regulatory requirements for validation protocols. Regularly review and update validation procedures based on performance data.
5. Insufficient Employee Training
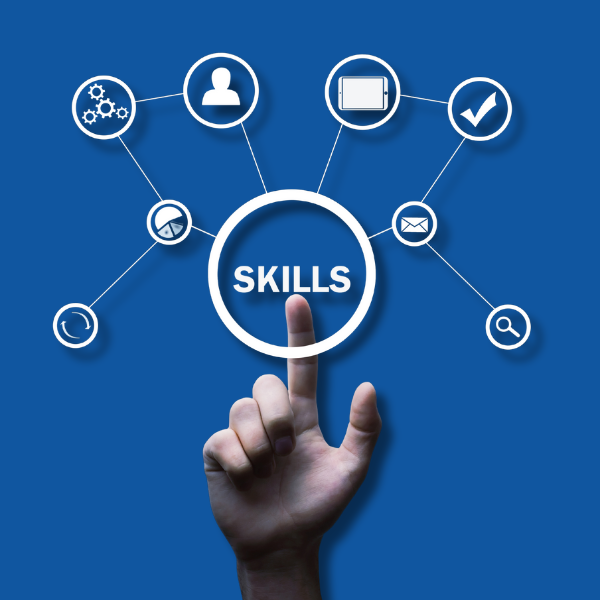
The Risk:
Untrained employees can introduce errors into production and QC inspections.
Solution:
Encourage a culture of proactive quality management and provide training and certification programs for employees.
6. Failure to Monitor Environmental Conditions
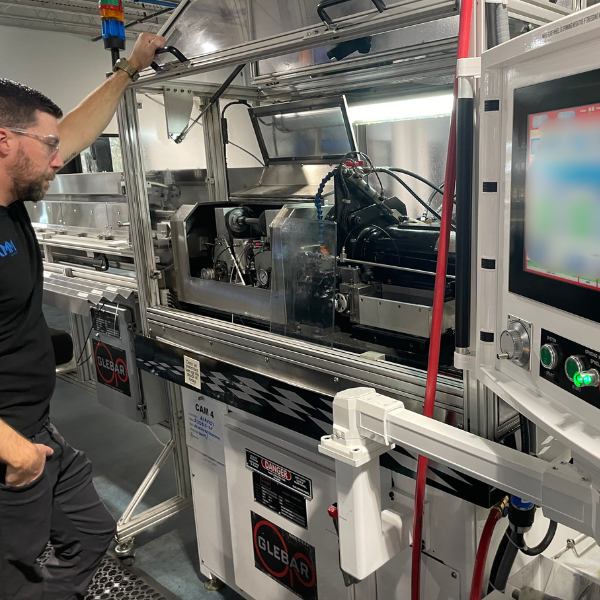
The Risk:
Variations in temperature, humidity, and particulate contamination can affect product integrity.
Solution:
Use environmental monitoring systems and regularly calibrate equipment to maintain optimal conditions.
7. Lack of Precision in Micro-Manufacturing
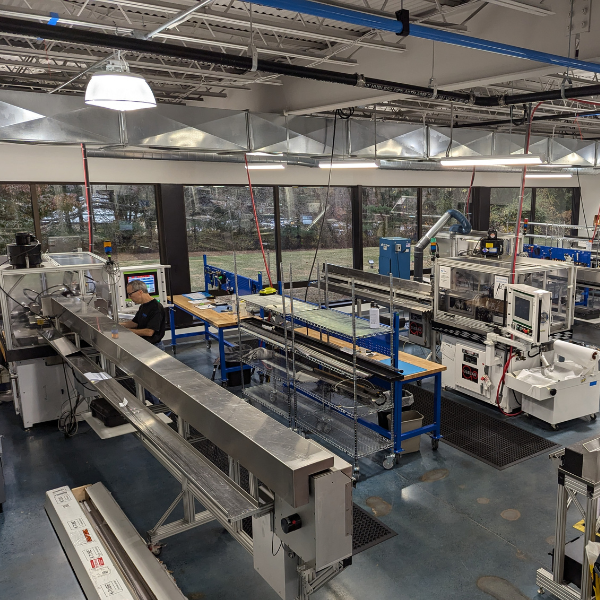
The Risk:
MedTech components often require ultra-precision machining and advanced grinding capabilities, where even micron-level deviations can compromise device functionality.
Solution:
Utilize advanced CNC and multi-axis grinding technologies. Invest in real-time measurement tools for process verification.
Avoiding these quality control pitfalls is essential for ensuring high precision and compliance in medical device manufacturing. By proactively addressing these challenges, manufacturers can enhance product reliability, streamline production, and maintain regulatory compliance.
As an “all-under-one-roof” contract manufacturing organization (CMO), KMM delivers on precision and the culture of quality needed for success. Let’s talk about your next project. Reach out today to see how our team can support your manufacturing needs.