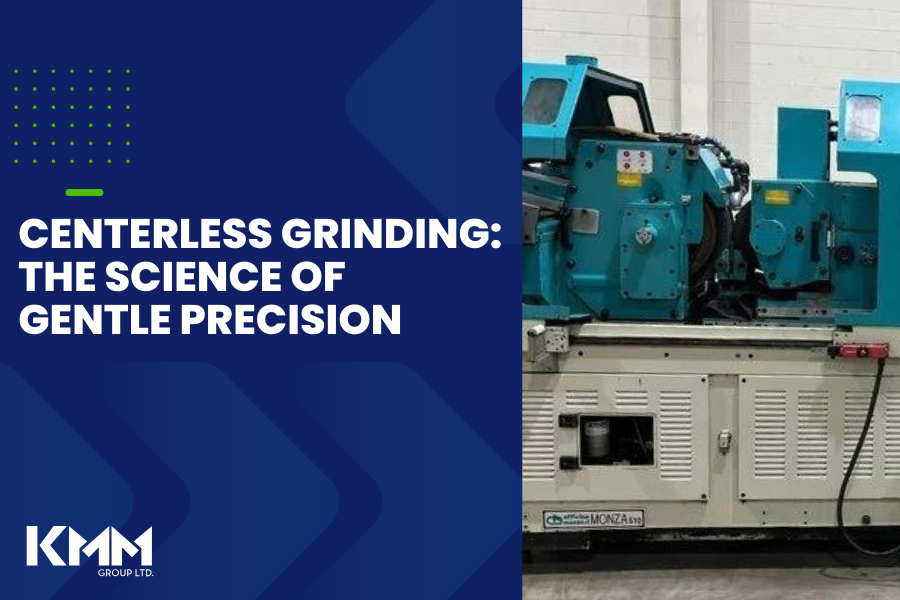
Remember those old-school pencil sharpeners bolted to classroom walls? You never had to worry much about precision while turning the crank to grind wood and lead to a useable point, you just needed a sharp pencil to survive math class. But what if the pencil lead had to be so accurate to fill in the test, that a traditional pencil sharpener no longer works. Suddenly, precision matters a lot.
That’s the difference between traditional and centerless grinding. Think of it like sharpening a pencil without gripping it tightly, instead, letting it settle naturally against the grinding wheels. The result? Unmatched precision and flawless symmetry, critical when manufacturing components where lives depend on fractions of a millimeter.
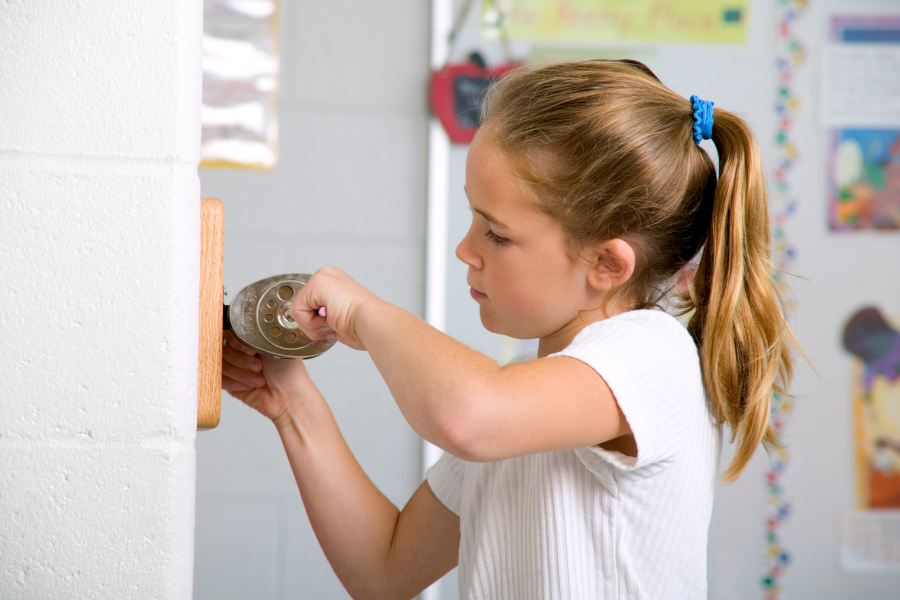
Why Traditional Grinding Falls Short
Traditional OD or ID grinding methods hold a workpiece on its centerline. When the part is rotated on its center, and a grinding wheel is brought in contact with it, the grinding wheel will remove an equal amount of material from both sides of the part. So, for every .001” the grinding wheel moves toward the part, it will remove a total of .002” from the diameter. As a result, there is a 2:1 ratio of material removal to grinding wheel movement.
Centerless grinding rewrites the rules of traditional grinding. Components rest gently against a regulating wheel, finding their perfect balance point. However, when a grinding wheel is introduced to the equation and begins to remove material from the part, the part falls away from the grinding wheel as it rotates and rests against the regulating wheel. For every .001” the wheel increments in, only .001” is removed from the diameter of the workpiece. Inherently, this process is twice as accurate as traditional OD or ID grinding as it produces a 1:1 ratio of material removal to grinding wheel movement.
Where Precision Feels Like Magic
Here’s what makes it so precise: a centerless grinder involves three key components:
- Grinding Wheel: Does the precision shaping/grinding.
- Regulating Wheel: Guides the speed and orientation of the component.
- Work Blade: Bears the weight of and supports the component.
Rather than forcing a workpiece to conform to the datum of its centerline, centerless grinding allows parts to align themselves naturally, and reference only the diameter which is being ground. This approach will naturally want to round and straighten a workpiece which can present huge obstacles when using more traditional grinding methods.
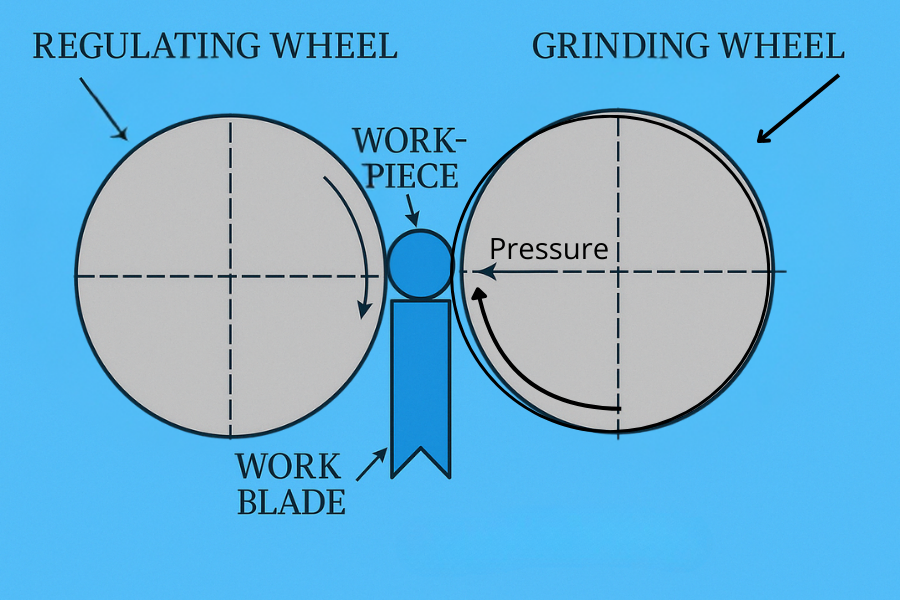
Challenges & Trade-offs. It's Not Easy Being Precise
As precise as it is, centerless grinding isn’t exactly a walk in the park. With no rigid support, operators must expertly juggle:
- Wheel speeds and dimensions
- Regulating wheel pressure and angles
- Precise blade alignment
It takes real skill, like balancing spinning plates without letting one wobble. Operators must rely on extensive experience, deep technical knowledge, and precise adjustments to master these challenges. Without skilled professionals guiding the process, achieving consistent precision is virtually impossible.
Real-World Precision: Achieving Bend-Free Guidewires
Precision grinding is crucial in creating perfectly straight bend-free guidewires. Imagine threading a delicate wire into the human heart or brain knowing there’s no room for error. Even the tiniest bend renders the guidewire ineffective.
Expert centerless grinding ensures each guidewire maintains flawless straightness and integrity, consistently meeting stringent industry demands. Curious about how KMM’s proprietary precision grinding methods resolve guidewire production challenges? Explore our guidewire grinding case study to see the science in action.
Types of Centerless Grinding: Which Method Fits You?
- Through-Feed Grinding: Think conveyor belt. This method is great for cylindrical parts, efficiently shaping thousands of components swiftly and uniformly.
- Hybrid Centerless Grinding – Guidewire grinding and Dedtru Grinding which present the opportunity to incorporate intricate features quickly and easily
- In-Feed Grinding: Ideal for complex or intricate geometries like custom medical implants or precision automotive components.
- End-Feed Grinding: Perfect for tapered parts, ensuring each component meets precise dimensional and shape criteria.
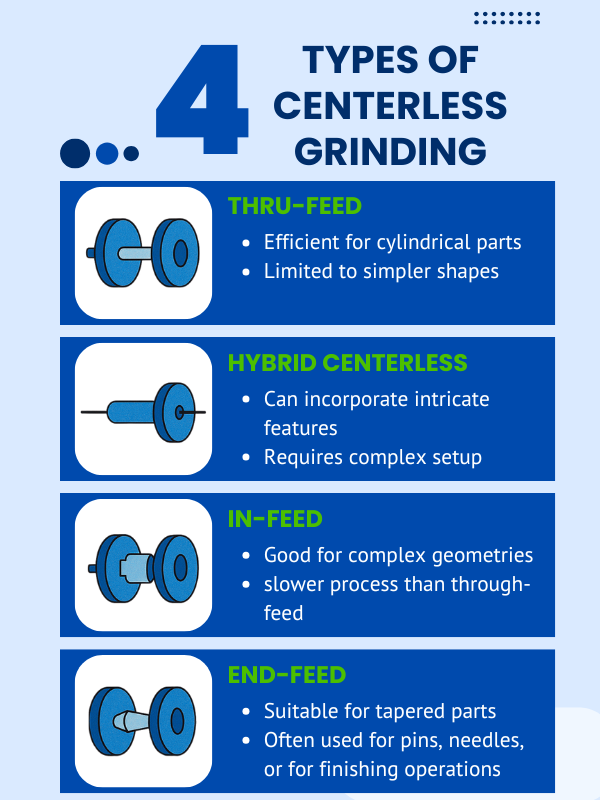
Why Manufacturers Love Centerless Grinding
- Micron-Level Precision: Unmatched accuracy for high-stakes applications in medical devices, aerospace, and automotive components.
- Efficient Production: Faster cycle times, boosting productivity and saving costs.
- Not Bound by Traditional Grinding Constraints: Traditional OD/ID grinding methods require rigid support, limiting their effectiveness on long, thin parts. Centerless grinding bypasses these limitations, making it ideal for grinding long, slender workpieces with ease.
- Flawless Surface Finish: Smooth finishes minimize friction, reduce wear, and enhance component longevity.
Take Your Precision Components to the Next Level
Precision is more than a buzzword it’s the difference between reliability and risk. Centerless grinding delivers precision, efficiency, and reliability, and at KMM Group, we specialize in overcoming your most challenging manufacturing hurdles.
Do you have parts keeping you up at night? Facing recurring issues like pigtailing, distortion, or inconsistent dimensions?
Contact KMM Group today. Let’s discuss your precision manufacturing challenges and discover how our expertise can turn your complex problems into simple solutions.
