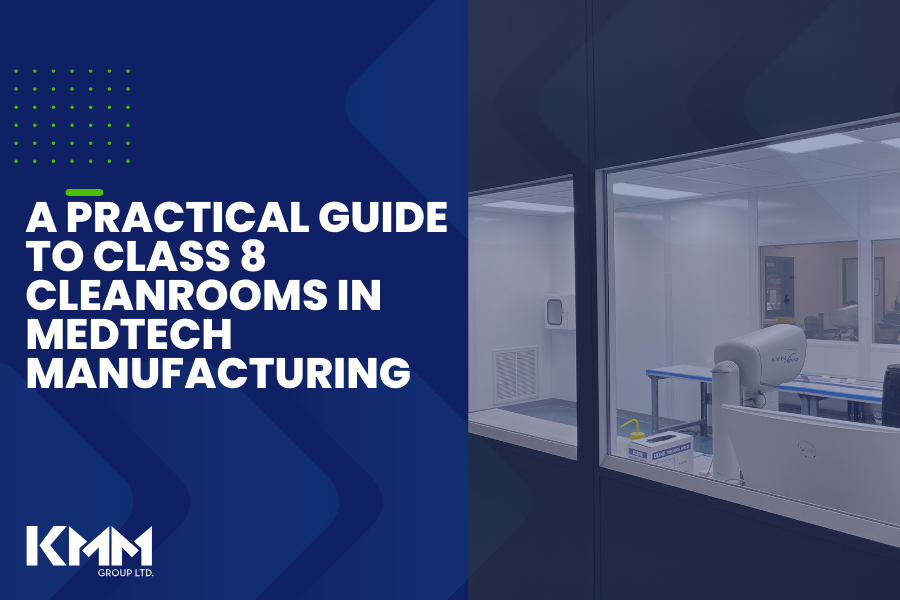
Why MedTech Relies on Class 8 Cleanrooms
MedTech products, especially those used in sensitive medical applications, require an environment that meets strict quality standards. This is where Class 8 cleanrooms come into play. As part of the ISO 14644-1 standards, Class 8 cleanrooms provide a controlled environment with a low level of airborne particulate contamination, which is essential for ensuring the highest quality and safety in the production of medical devices and components.
For MedTech manufacturers and OEMs (Original Equipment Manufacturers), understanding the role and requirements of Class 8 cleanrooms is key to improving product quality and meeting regulatory demands. What follows is a practical guide on the importance of Class 8 cleanrooms, how they function, and how they contribute to the manufacturing of high-quality medical products.
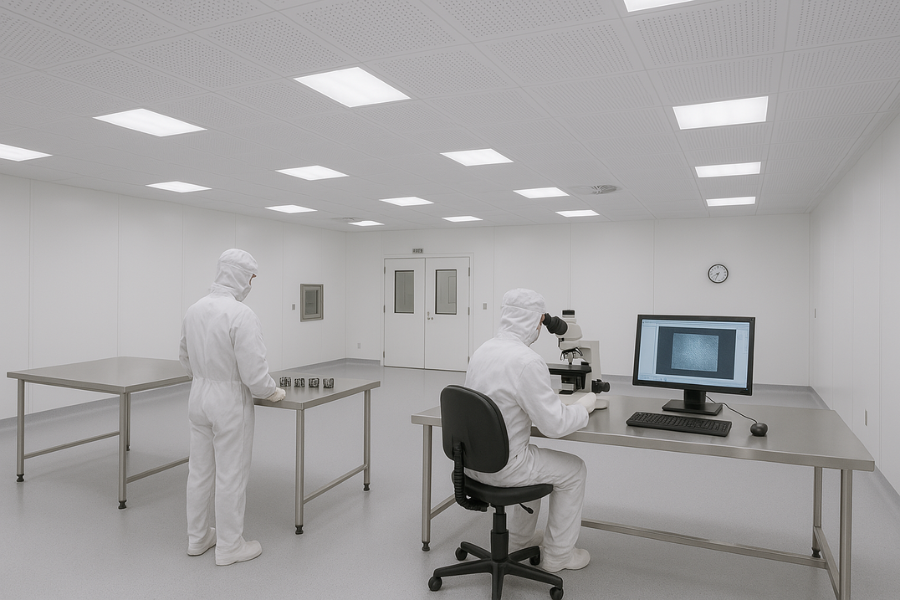
What Defines a Class 8 Cleanroom
A Class 8 cleanroom is a controlled environment where the concentration of airborne particles is regulated to a maximum of 3,520,000 particles per cubic meter, with particle sizes greater than or equal to 0.5 microns. These cleanrooms are part of the ISO Cleanroom Standards developed by the International Organization for Standardization (ISO). The classification system is designed to ensure the air quality in a cleanroom is safe for the production of sensitive products, such as medical devices and pharmaceuticals.
An ISO-certified cleanroom meets the specific requirements set forth in ISO 14644-1, which dictates air quality, cleanliness protocols, and monitoring systems. These standards are essential for industries where contamination could lead to compromised product safety or performance. Class 8 cleanrooms meet stringent guidelines for environmental monitoring, including airflow velocity, temperature, humidity, and particle count, to maintain optimal conditions for MedTech manufacturing.
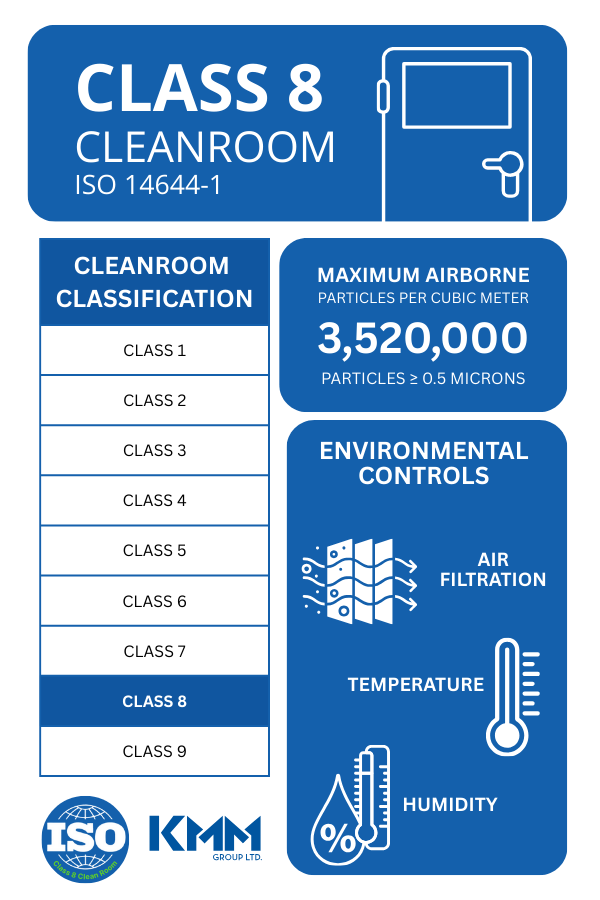
Reducing Contamination Risks
MedTech products, such as implants, surgical instruments, and diagnostic devices, must meet the highest standards of hygiene and sterility. The tiniest particle of contamination can lead to device failure or adverse patient outcomes. Class 8 cleanrooms play a critical role in preventing the introduction of contaminants during the manufacturing process. With strict air filtration and environmental control, these cleanrooms significantly reduce the risk of particulate contamination, ensuring that products meet regulatory requirements and perform as intended.
Enhancing Precision and Quality Control
MedTech manufacturing requires precise fabrication, often at micron or nanometer levels. The controlled environment provided by Class 8 cleanrooms enables manufacturers to maintain the necessary conditions for high-precision processes like micromachining, laser cutting, and precision assembly. These environments contribute to tighter tolerances and better quality control by eliminating the variability that airborne particles can introduce into the manufacturing process.
Compliance with Regulatory Requirements
MedTech manufacturers must adhere to rigorous regulations set by agencies like the FDA (Food and Drug Administration) and ISO 13485, which outlines the quality management systems for medical device manufacturers. Using an ISO-certified cleanroom ensures compliance with these regulations, which are crucial for obtaining product approvals and maintaining certifications. For MedTech OEMs and contract manufacturers, ensuring cleanroom standards can be the difference between successful product development and costly delays.
Improving Product Performance and Reliability
Class 8 cleanrooms contribute to the reliability and performance of MedTech products. By minimizing contamination and maintaining controlled environmental conditions, manufacturers can ensure that their products function correctly under real-world conditions. For instance, in the case of surgical instruments, any contamination could compromise functionality, leading to operational failures or even patient harm. Cleanrooms help mitigate such risks, promoting safer, more reliable products.
Selecting the Right Cleanroom for Your Manufacturing Needs
Not all cleanrooms are created equal. While Class 8 cleanrooms are well suited for many MedTech applications, it’s important to assess the specific needs of your production processes. For high-risk, high-precision applications, you might also require Class 7 or Class 6 cleanrooms. Work with an experienced contract manufacturer who understands the nuances of cleanroom standards and can help design a cleanroom strategy that meets your product requirements.
Continuous Monitoring and Maintenance
Maintaining the integrity of a Class 8 cleanroom requires ongoing monitoring and strict adherence to maintenance protocols. Regular testing for airborne particles, air pressure balance, and filter integrity are essential to ensure the cleanroom continues to meet ISO standards. Partnering with a reliable contract manufacturer ensures that cleanroom environments remain compliant and optimized for high-quality MedTech manufacturing.
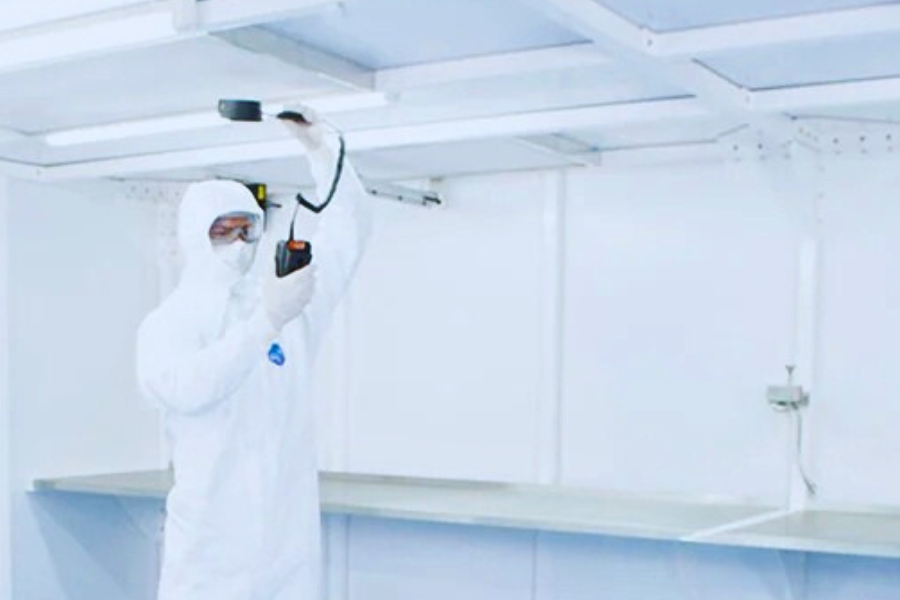
Class 8 Cleanrooms an Essential Investment
Class 8 cleanrooms are a cornerstone of quality manufacturing in the MedTech industry. They provide the controlled environment necessary for producing high-precision, reliable, and safe medical devices that meet regulatory standards. Whether you’re a MedTech OEM or a contract manufacturer, investing in a well-maintained, ISO-certified cleanroom can help ensure your products meet the highest quality standards and reduce contamination risks.
If you’re working on a MedTech project that requires a Class 8 cleanroom environment, contact KMM Group today to discuss how our expertise and state-of-the-art cleanroom facilities can support your manufacturing needs and ensure optimal results for your products.