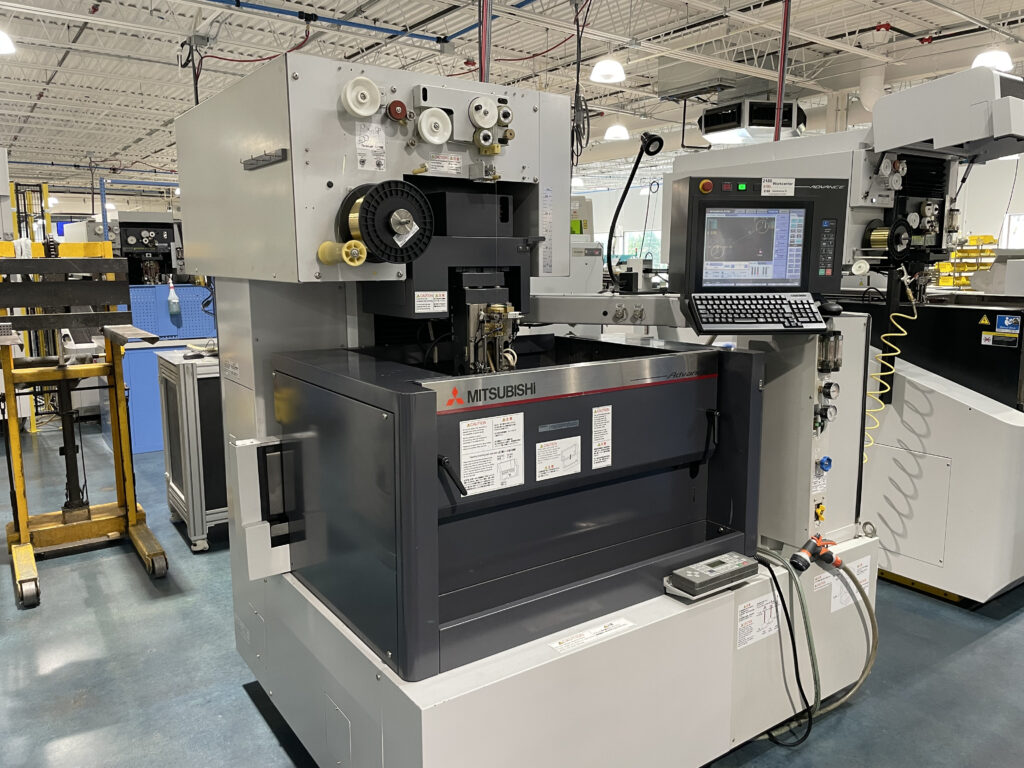
Producing strong and durable components is essential for the success and safety of critical missions and applications in fields like medtech, space exploration, and aerospace. When lives and investments are on the line, parts must be machined to endure the demands of a human body, the grueling conditions of space, or the high stress and temperatures of aircraft. Wire EDM is a high-precision process that uses electrical discharges to accurately erode the material while preserving a part’s strength and integrity and contributing to its longevity. In this post, we’ll explain this crucial strength-promoting advantage of wire EDM and how to maximize your product design for maximum part durability.
How Wire EDM Enhances Part Durability
Through precise material removal, minimal recast layers, stress-free machining, and other strength-enhancing capabilities, wire EDM produces strong and durable parts, promoting their critical safety and reliability.
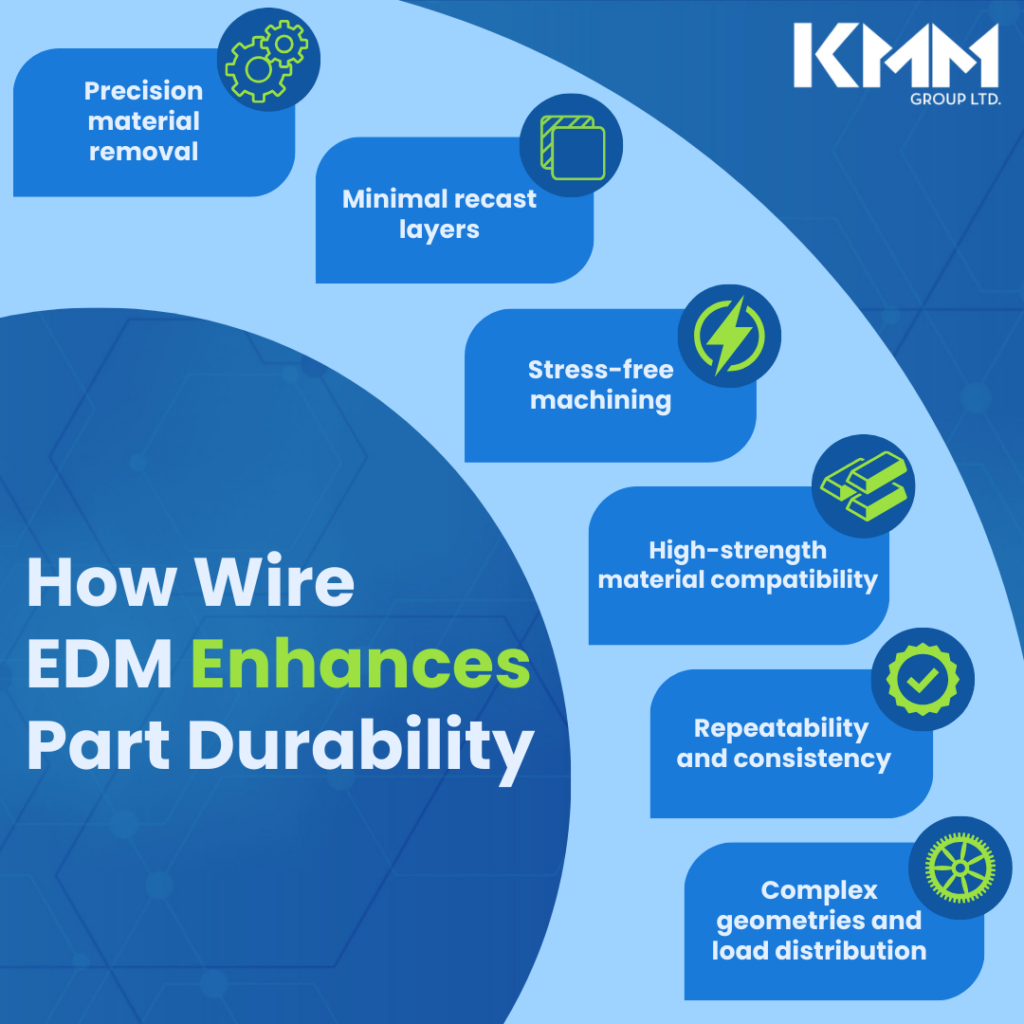
- Precision material removal: Wire EDM’s high precision ensures components fit together without gaps or misalignments. This accuracy enhances performance and longevity by minimizing assembly issues and ensuring seamless interaction between parts.
Minimal recast layers: Wire EDM minimizes the formation of recast layers, areas where molten metal particles cool and harden on the surface. These hard, brittle layers can introduce weaknesses into the part. Wire EDM preserves the original material properties by curtailing recast layers, contributing to a more robust and durable component.
Stress-free machining: The wire EDM process uses electrical discharges to erode material without physical contact, avoiding mechanical stresses and potential microcracks. This approach preserves the material’s inherent strength, enhancing the part’s overall durability. It also eliminates weak spots that could lead to premature wear or failure.
High-strength material compatibility: Wire EDM can handle high-strength materials, including hard-to-machine alloys like titanium, Inconel, and stainless steel. This capability ensures that components maintain integrity and performance in demanding environments for enhanced durability and longevity.
Repeatability and consistency: Wire EDM ensures each part is produced with precise and consistent tolerances, eliminating variability. This reliability in manufacturing enhances the structural integrity and strength of the machined parts.
Complex geometries and load distribution: Wire EDM’s ability to impart intricate features allows engineers to design parts that can better distribute loads across the component. This reduces stress concentrations in any one area, which helps prevent premature wear, deformation, or failure. By evenly distributing stress, components maintain their structural integrity and durability in demanding conditions.
5 Product Design Considerations to Maximize Part Durability
While wire EDM is designed to produce tough and long-lasting parts, it’s important to consider potential weaknesses during product design to ensure maximum durability. Here are several considerations:
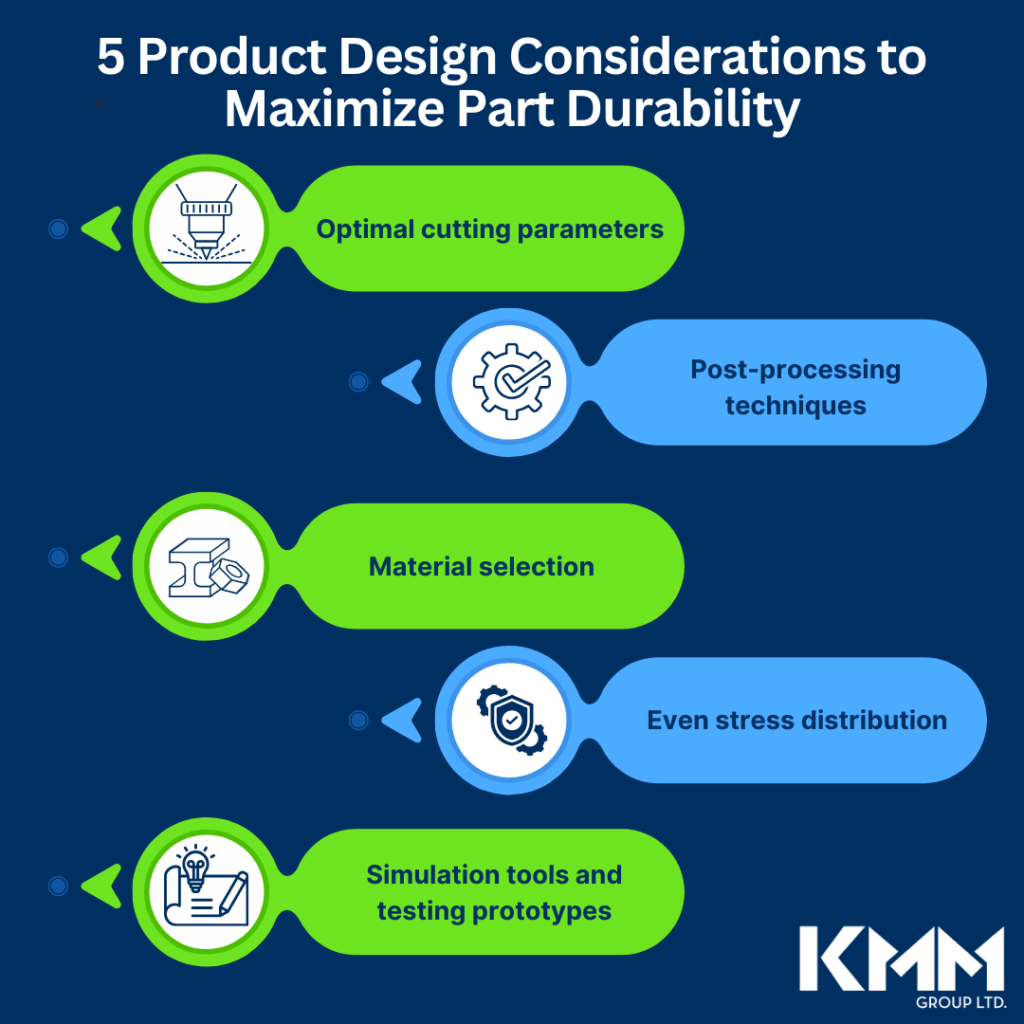
Optimal cutting parameters: Collaborate with experienced wire EDM operators to fine-tune cutting parameters—such as electrical discharge intensity and cutting speed—to reduce the thickness of recast layers further and improve material resilience.
Post-processing techniques: Techniques like polishing or chemical etching can remove any remaining recast layers, enhancing your components’ durability and quality.
Material selection: Ensure material compatibility with wire EDM while ensuring the necessary strength, toughness, and corrosion resistance for the application.
Even stress distribution: Design components to evenly distribute stress to enhance durability and resistance to fatigue.
Simulation tools and testing prototypes: Using simulation tools and testing prototypes, identify potential weaknesses and areas for improvement to ensure the component’s performance and durability under various conditions.
Learn more about designing die components for wire EDM on the blog.
Start Building Tougher Components with Our Wire EDM Experts
Wire EDM produces stronger, tougher parts, enhancing durability, reliability, and safety. By integrating wire EDM into your production process, you can harness its many technical advantages and long-term benefits. As industry leaders in wire EDM, we offer a state-of-the-art facility, operator excellence, and robust quality controls to ensure maximum part precision and durability. Contact us to discover how wire EDM can strengthen your next mission-critical product design.