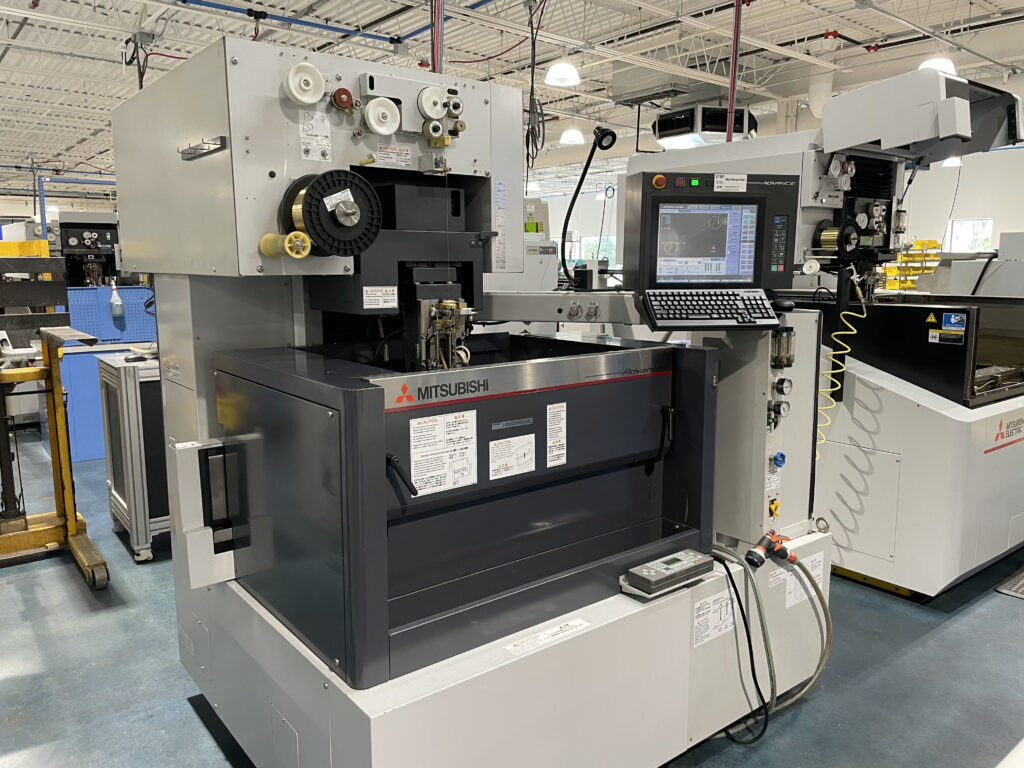
Wire EDM is an advanced precision manufacturing process that unlocks endless possibilities for creating intricate geometries and fine details in parts. This technology is a game-changer for industries that demand high precision and intricate component designs, enabling extremely accurate machining of “problem” parts. In this post, we’ll explore the magic of wire EDM, showcasing its transformative precision and ability to expand the horizons of design and creativity.
Redefining Precision
Wire EDM redefines precision in modern manufacturing by offering unique capabilities that traditional machining methods cannot match. It enables the production of complex geometries and fine details with exceptional precision and accuracy, optimizing part performance, consistency, and reliability. This technology ensures components meet the highest quality standards, reducing the risk of defects and enhancing the overall functionality and durability. It allows for:
- Intricate cuts: Produce complex and detailed cuts often impossible with traditional methods.
- Fine details: Achieve highly precise and extremely fine features using .002” diameter wire, allowing for the finest details in small and intricate parts. This is ideal for producing high-precision micro-sized components.
- Thin walls: Machine parts with extremely thin walls, which are difficult to achieve with conventional techniques, ensuring structural integrity and minimizing material usage.
- Ultra-small internal radii: Achieve inside corner radii as small as .0013”, allowing for the creation of intricate and delicate part features.
- Precise contours: Create precise and complex contours, ensuring each part meets exact specifications and performs reliably in its intended application. With Wire EDM, you can be confident in the performance of your parts.
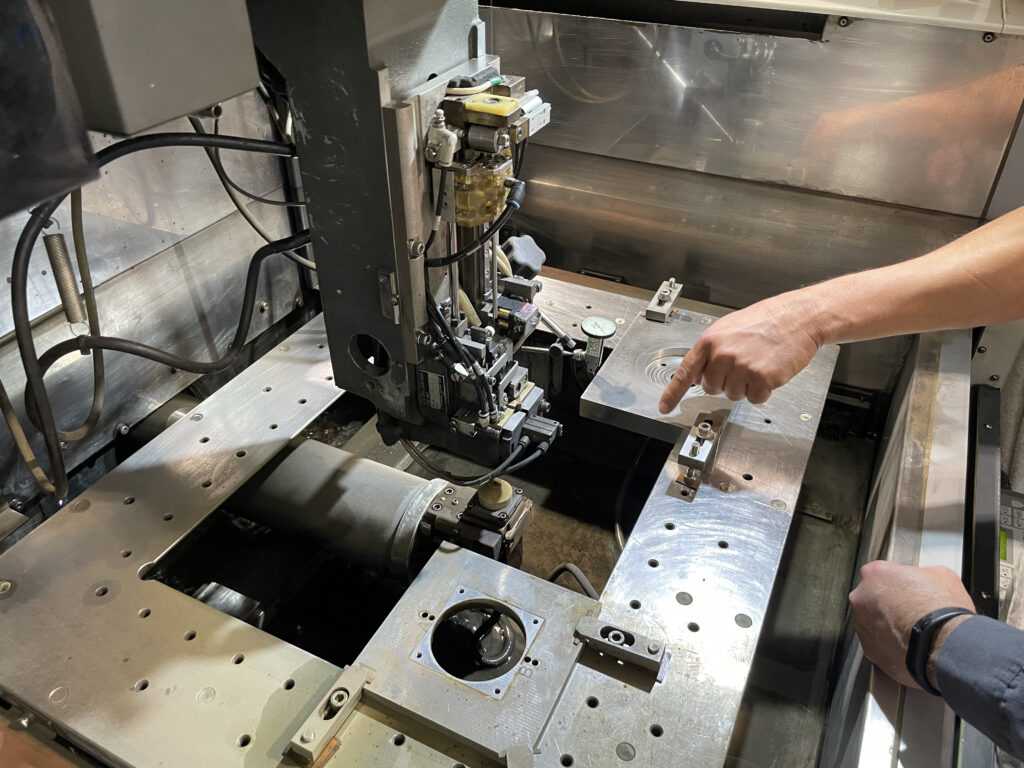
Enhancing Design & Innovation
Wire EDM technology revolutionizes engineering by enabling innovative designs. For instance, it allows the creation of complex medical implants with integrated functionalities and can dramatically improve the performance and efficiency of existing designs. Wire EDM transforms the landscape of design and innovation by achieving:
- Complex geometries: Machine parts with intricate interior geometries, provided there is a straight surface from the top to the bottom of the part.
- Tapered features: Create tapered features that go through a part, vital for innovative designs that require intricate and varying thicknesses.
- High-aspect ratios: Produce parts with tall and narrow features, such as microchannels, fins, or narrow slots.
- Material versatility: Wire EDM excels without concern for material hardness, consistently delivering high precision with challenging materials like Hastelloy, Inconel, and other hard-to-machine alloys.
- Long depth-to-width ratios: Achieve very long depth-to-width ratios, ideal for parts with deep and narrow features, such as in molds or deep cavities.
Unleashing Creativity
Wire EDM promotes creativity by providing design engineers with near-unfettered freedom and flexibility. It empowers them to explore and realize their most imaginative and complex ideas, pushing the boundaries of traditional design. This technology allows engineers to bring their most innovative visions to life. With wire EDM, engineers can create:
- Intricate and artistic designs: Create highly detailed components previously impossible or impractical with traditional methods.
- Highly customized solutions: Develop custom parts tailored to specific applications and requirements, enhancing functionality and performance.
- New shapes and forms: Push the boundaries of conventional design to explore and implement groundbreaking ideas and concepts.
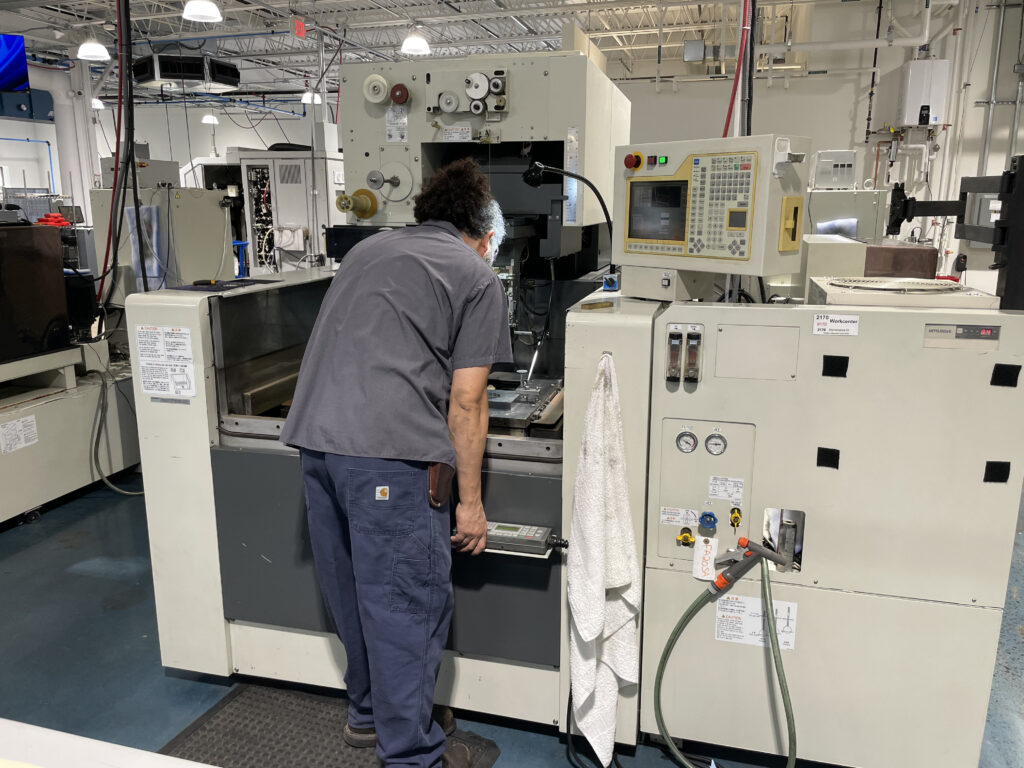
Step Inside Wire EDM’s Precision and Mastery
Wire EDM’s ability to achieve high-aspect ratios, fine details, complex geometries, and other intricate features with unparalleled precision is rooted in its unique operating principles, advanced technology, and operator expertise. Here’s how the magic happens:
- Small, controlled material reduction: Intense heat melts and vaporizes material in precise amounts, ensuring integrity during complex cuts.
- Stress-free machining: Cuts without mechanical stress, preserving and relieving stress in delicate components.
- Advanced technology: Sophisticated control systems and precision machinery ensure accuracy and repeatability.
- Operator expertise: Skilled operators optimize performance, ensuring precision and quality in complex and intricate parts.
Whether working with ultra-small features, thin walls, or hard-to-machine materials, wire EDM can bring your most innovative and intricate designs to life with exceptional accuracy and reliability. Contact us to put wire EDM to work on your next project.