Medical guidewires play a pivotal role in the healthcare industry, acting as the “guides” for life-saving devices used in procedures like aneurysm coiling, interventional cardiology, and thrombus extraction. For Original Equipment Manufacturers (OEMs) and engineers, understanding the guidewire manufacturing process ensures better product selection and optimization.
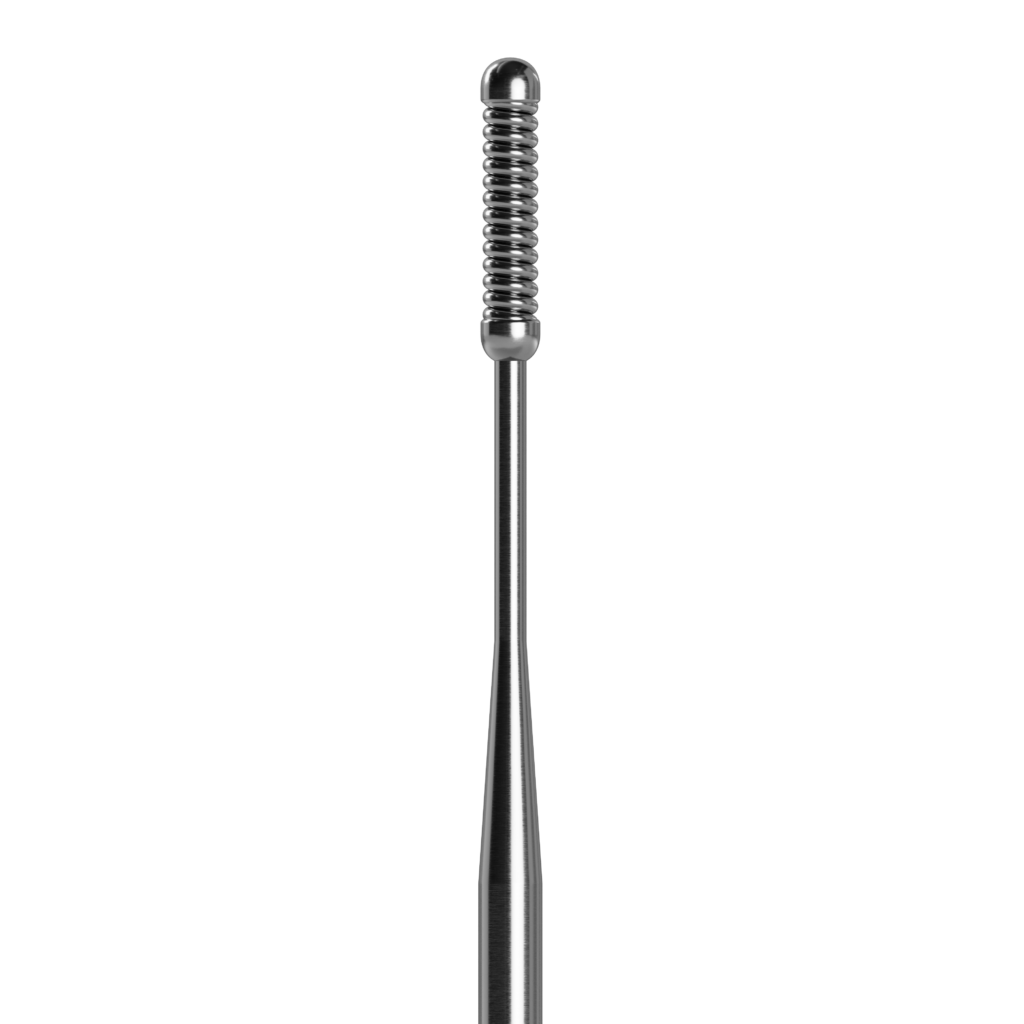
What Are Medical Guidewires?
Medical guidewires are thin, flexible wires designed to navigate the intricate anatomy of the human body. These wires provide support and precision for catheters, stents, and other interventional devices.
Importance in Medical Applications
Guidewires are indispensable in procedures for neurovascular, cardiovascular, and peripheral vascular interventions. Their ability to maneuver through complex structures makes them vital in angioplasty, neuromodulation, and clot retrieval.
Materials Used in Medical Guidewires
The choice of material is critical to the performance and durability of medical guidewires. Each material offers unique properties tailored to specific medical applications.
Stainless Steel (SST)
- High strength and durability.
- Excellent torque response for precise navigation.
Nickel-Titanium (NiTi)
- Known for its flexibility and shape memory.
- Ideal for navigating tortuous anatomies without kinking.
Exotic Alloys and Precious Metals
- MP35N (Nickel-Cobalt alloy): Exceptional strength and corrosion resistance.
- Hastelloy: For highly specialized use cases requiring extreme durability.
- Precious metals: Occasionally used for conductivity in specific devices.
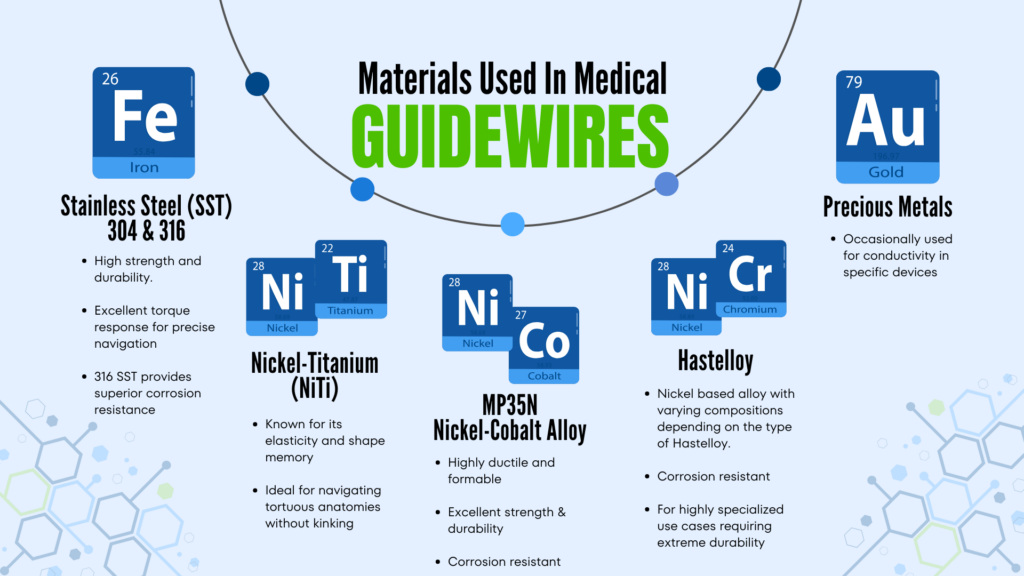
Overview of the Medical Guidewire Manufacturing Process
The manufacturing process involves several precise steps to produce wires capable of withstanding medical demands. From material selection to final inspection, every stage emphasizes accuracy, consistency, and quality.
Highly Specialized Micro-Grinding Techniques
Guidewire production relies heavily on precision grinding to shape wires into complex geometries. Two key grinding methods include:
Centerless Mode
- Ideal for less complex geometries.
- Utilizes a wider grinding wheel for high throughput and precision.
Outer Diameter (OD) Mode
- Best for intricate geometries with narrow grinding wheels.
- Achieves ultra-precision by feeding the wire through hydrostatic bushing.
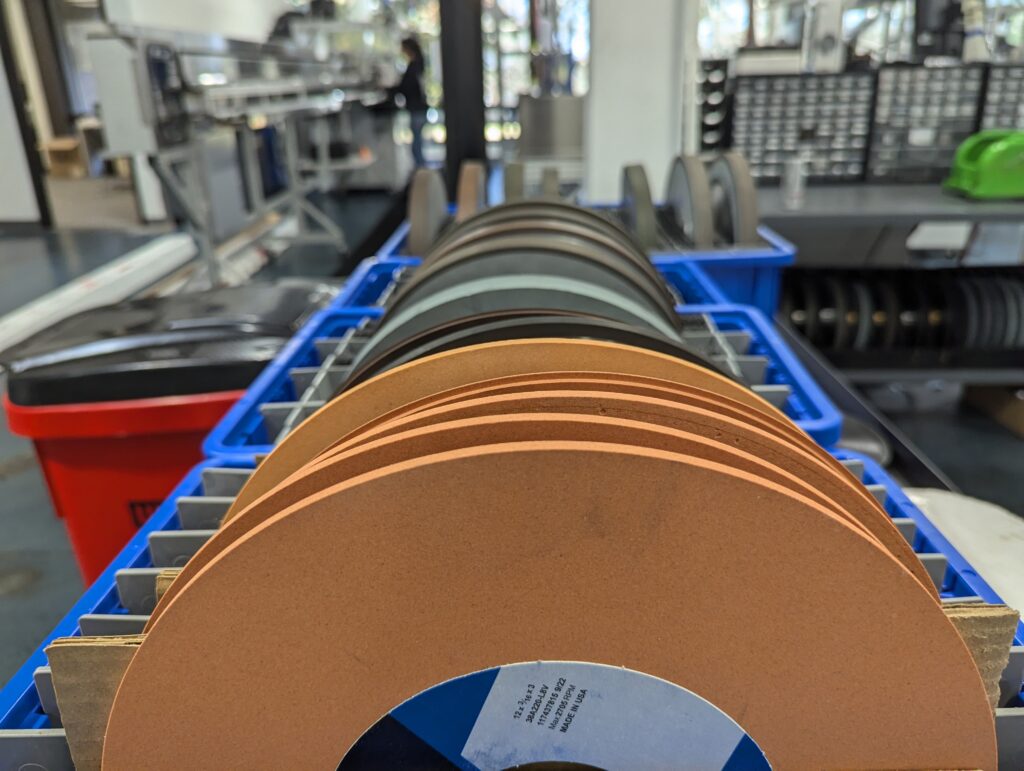
High-Tech Equipment in Medical Guidewire Manufacturing
Modern grinding machines are indispensable for creating medical guidewires with diameter tolerances as small as .0001 inches and ground length tolerances to ±0.005 inches.
Precision and Efficiency
Skilled operators use these machines to control speed, rotation, and pressure, ensuring consistent quality even for the smallest diameters.
Importance of a Rigorous Quality Management System (QMS)
A robust QMS ensures every medical guidewire meets stringent safety and performance standards.
Key Quality Control Processes
- Continuous monitoring using wire profile inspection equipment.
- Skilled technicians verify every production step.
Certifications and Compliance (ISO 13485, FDA)
Our ISO 13485 certification and FDA registration underscore our commitment to quality and compliance, offering peace of mind to OEMs.
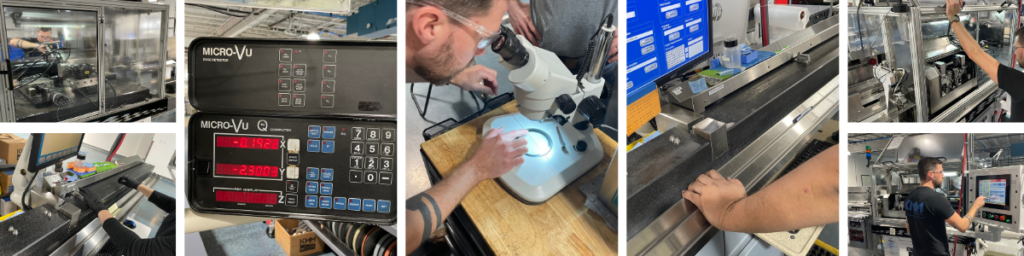
Challenges in Manufacturing Medical Guidewires
Manufacturing guidewires is not without hurdles. Challenges like maintaining diameter consistency, avoiding material defects, and ensuring operator precision require innovative solutions and advanced equipment.
Case Study: Bend-Free Guidewire Solution
When a biotech firm faced supply chain disruptions from bent guidewires, we developed a precision manufacturing solution. Our process stabilized their production, enabling them to scale confidently.
Why Choose Us for Your Medical Guidewire Needs?
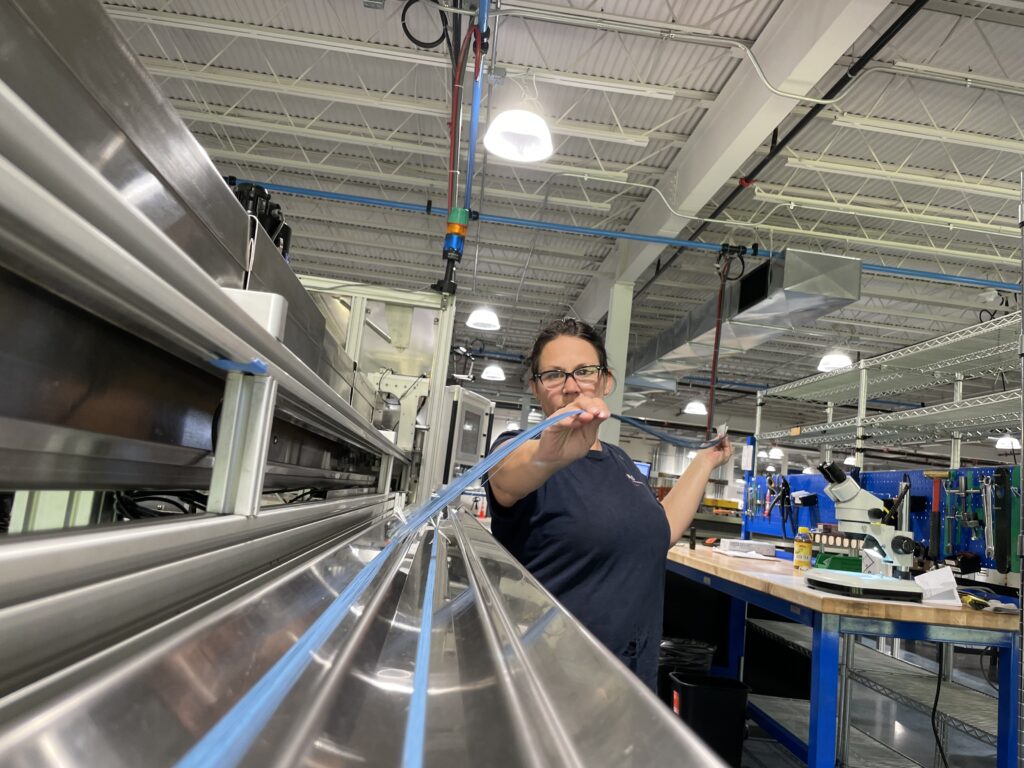
Expertise and Experience
With decades of expertise, our team excels in solving complex manufacturing challenges.
Rapid Prototyping and Problem Solving
Our in-house R&D and rapid prototyping services allow OEMs to bring products to market faster, ensuring seamless integration into production.
FAQ
They are made of materials like stainless steel, Nickel-Titanium, and MP35N, tailored to specific applications.
Medical guidewires can have diameter tolerances as small as .0001 inches and ground length tolerances to ±0.005 inches.
Precision ensures the guidewire can navigate complex anatomical structures safely and effectively.
Quality control ensures every wire meets safety and performance standards, reducing the risk of failure.
Medical guidewires are critical components in modern healthcare, requiring unparalleled precision and quality. With state-of-the-art equipment, a rigorous QMS, and a dedicated team, we provide solutions that help OEMs meet the demands of life-saving medical devices. Contact us today to learn how we can support your manufacturing needs.