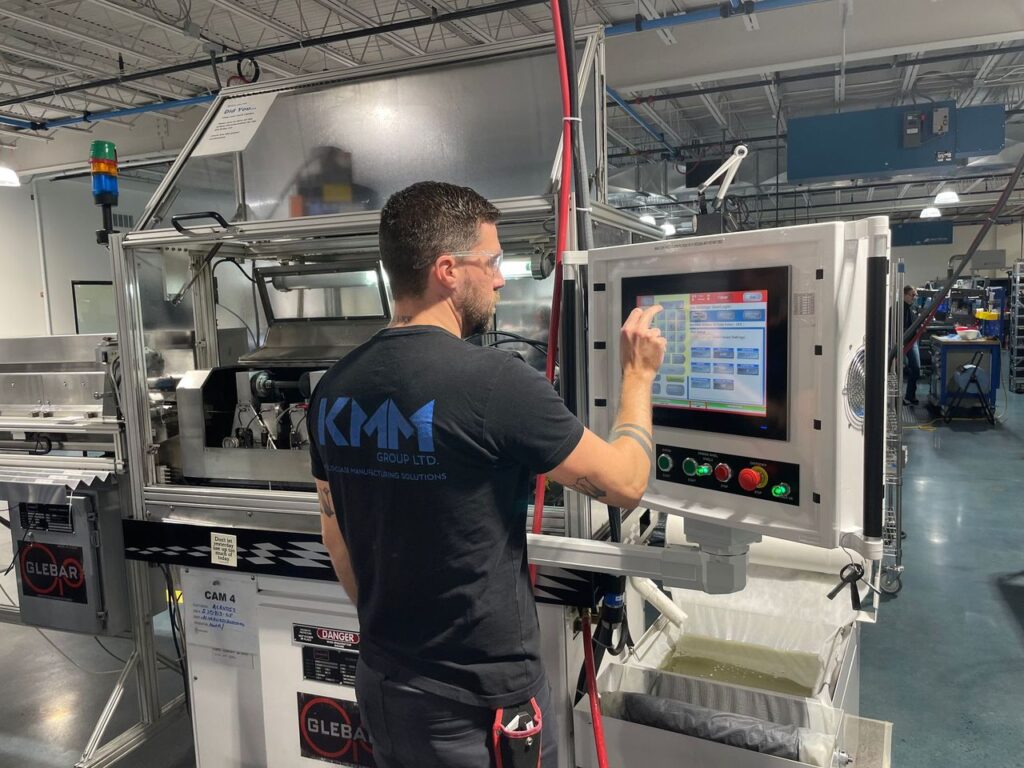
Guidewire grinding combines the accuracy of centerless grinding with the intricacies of Swiss screw machining. While this fusion brings together the best of both worlds, it also introduces unique and complex challenges that push the boundaries of precision manufacturing in the medtech sector. This post highlights a few of the hurdles unique to guidewire grinding and explores specialized solutions to overcome them.
1. Surface Finishes: The One-Pass Challenge
Unlike traditional grinding on a centerless lathe or mill, where multiple passes can refine a workpiece, guidewire grinding demands surface finish perfection in a single pass. This one-and-done transition from raw wire to finished dimension, especially with tight tolerances, highlights the need for exceptional precision and accuracy. Meeting this challenge requires innovative engineering and technology solutions to achieve the desired finish in one shot.
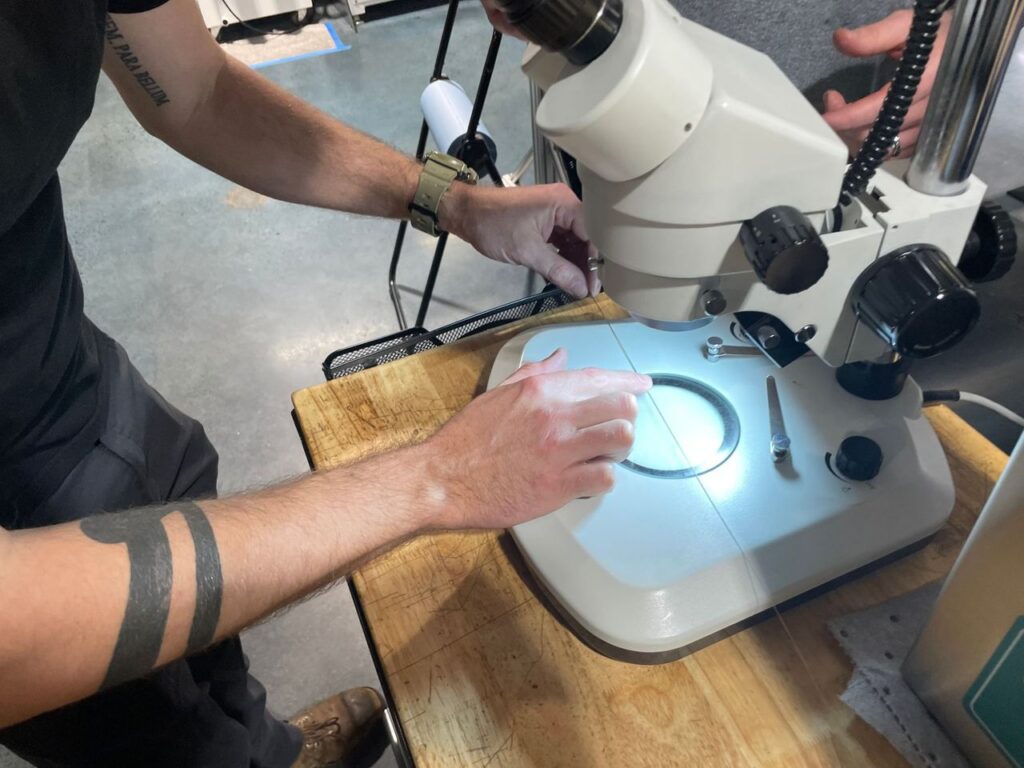
2. Programming Limitations: The Creative Challenge
Specialty guidewires often feature unique geometries, such as flats, triangles, or tapers, that pose significant machine programming challenges. With only a single tool at their disposal, engineers and operators must creatively navigate these limitations to impart the desired features onto the wire. As a result, crafting these specialty guidewires demands inventive approaches to the grinding process and machine programming, ensuring both innovation and cost-efficiency.
3. Difficult Materials: The Adaptation Challenge
Working with common guidewire materials such as nitinol, stainless steel, and titanium requires tailored adaptation strategies catering to their distinct properties. Nitinol’s toughness, for instance, can wear down grinding wheels quickly, necessitating super abrasive diamond wheels to minimize tool wear. Stainless steel poses challenges with internal stresses that can cause a corkscrew-shaped deformation known as the “pigtail” effect. Combatting this involves strategies like using specially formulated stress-resistant stainless steel and applying precise thermal treatments to alleviate these stresses without compromising the material’s integrity, among other technical solutions. Titanium, known for its difficulty maintaining a surface finish, requires specialized grinding techniques to avoid heat buildup and surface damage, ensuring a smooth finish.
Discover how we successfully tackled material challenges to produce flawlessly straight vascular guidewires when others faced difficulties.
4. Guidewire Size: The Equipment Challenge
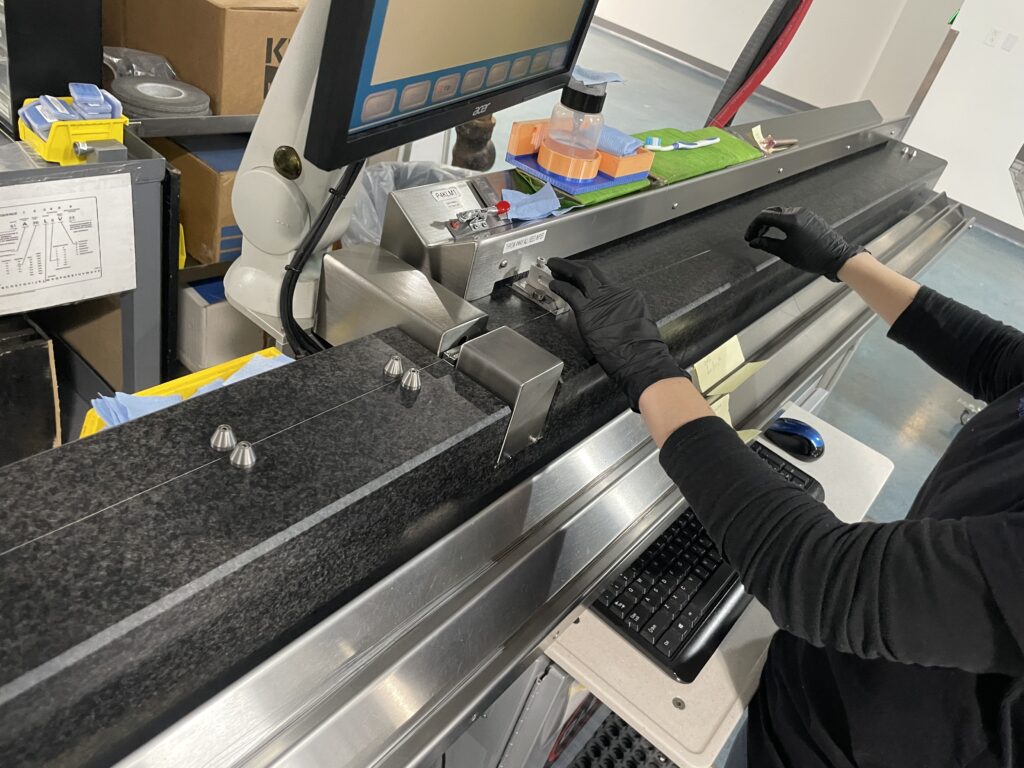
Guidewire grinding equipment is typically designed to handle wires no thicker than 1/16”, presenting a challenge for larger diameters. While limiting in size, this constraint is a byproduct of the equipment’s focus on precise, fine-detail work, ensuring exceptional precision for slimmer profile wires.
5. Tooling Challenges: The Wear and Tear Challenge
Tool wear, particularly on parts like the support blade and fixtures, is a significant issue in guidewire grinding, especially when working with abrasive materials requiring tight timelines. The need to frequently replace tooling can cause considerable downtime and drive up costs. However, adopting innovative tooling designs and investing in advanced abrasive technologies can prolong tool life and minimize the frequency of replacements. Our efforts to optimize grinding wheels have significantly improved outcomes, doubling our throughput in one instance by refining abrasive types and customizing grinding wheel formulations.
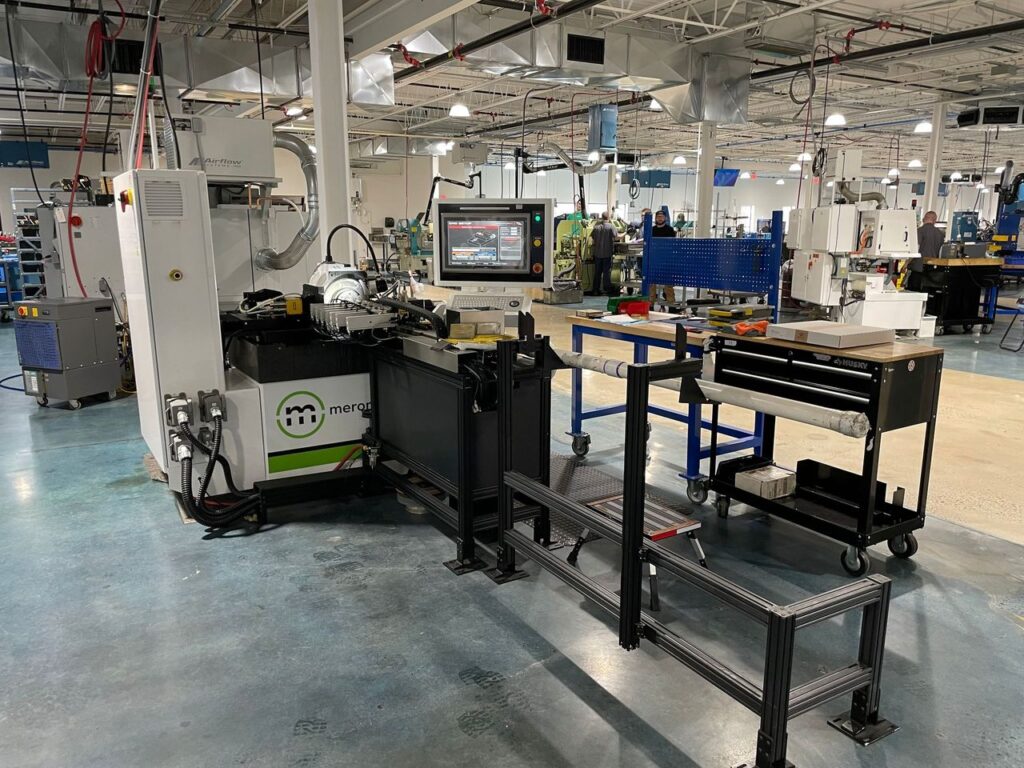
6. Ambient Conditions: The Environmental Challenge
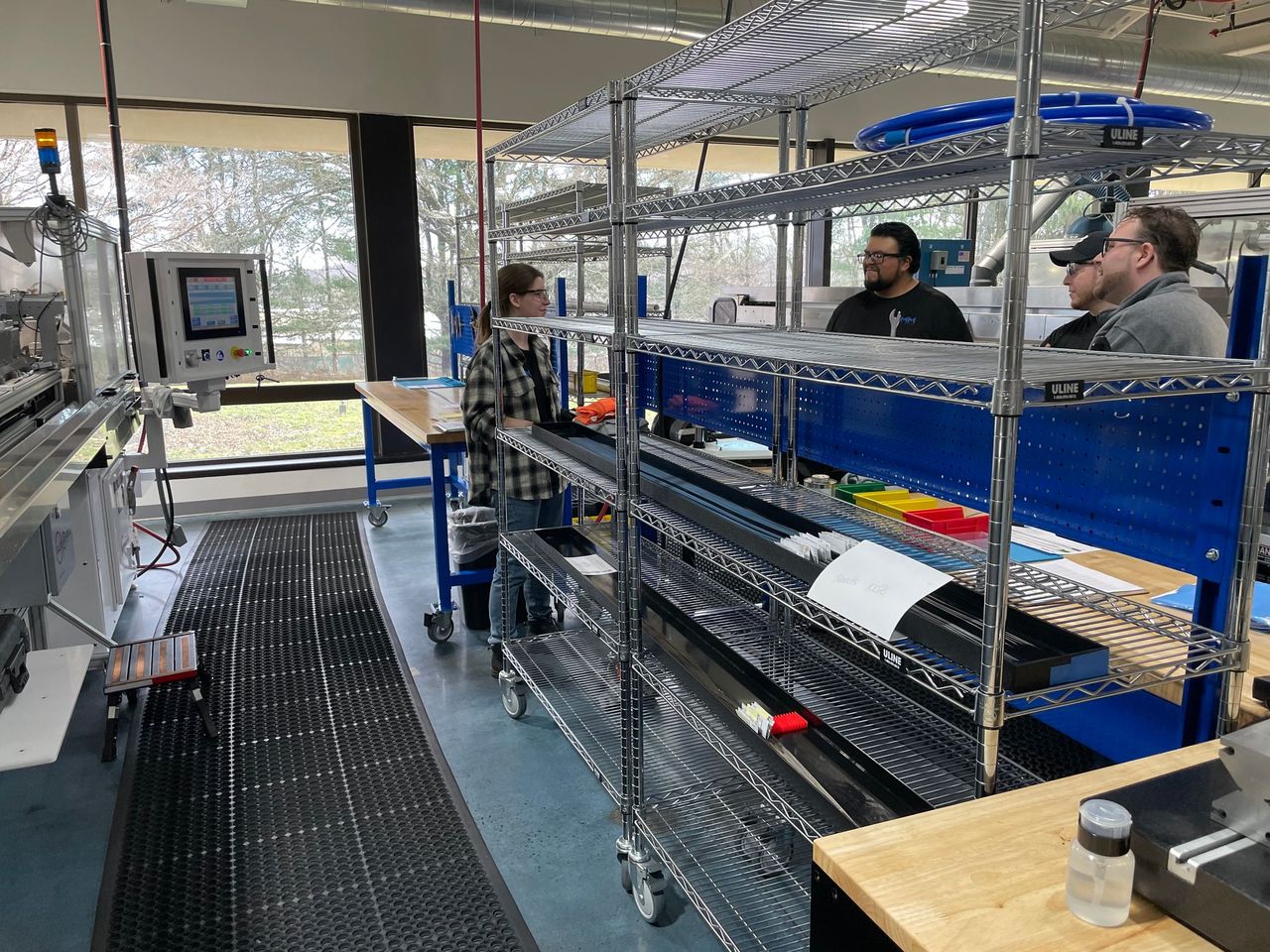
Even atmospheric conditions can impact the precision of guidewire grinding. Variations in temperature and humidity can significantly affect tight tolerances, making it challenging to maintain consistency. When we were first settling into our new state-of-the-art facility, we noticed that every time a door opened, the guidewire grinding machines went off-kilter, underscoring the sensitivity of the process to environmental conditions. Closely monitoring to maintain stable atmospheric conditions can significantly reduce disruptions, ensuring our grinding processes achieve the necessary precision and quality for reliable guidewires.
Ensuring Precision: The Role of Quality Control
Recognizing these guidewire grinding-specific challenges, implementing a robust quality control system under an experienced director of quality is essential to ensure that guidewires meet precise specifications consistently. This comprehensive approach to overcoming the unique challenges of guidewire grinding highlights the intricate precision and efficiency necessary for manufacturing life-saving devices and accelerating their market availability.
Unlocking the Science of Manufacturing Precision Guidewires
Guidewire grinding embodies our commitment to unlocking the science of manufacturing. Through innovative solutions, we continuously push the boundaries of what is possible in the pursuit of precision. Our dedication to exploring and understanding the underlying scientific principles of each material and process enables us to refine our techniques and technologies, further enhancing the quality and reliability of our parts.
Head to our blog for more on what to know before starting a guidewire grinding project, and reach out to learn more about how our expertise in precision guidewire grinding can help you navigate production complexities with accuracy and cost-efficiency.